How To Prevent And Manage Temperature Excursions In Clinical Trials
By Ana-Zeralda Canals Hamann, Debiopharm
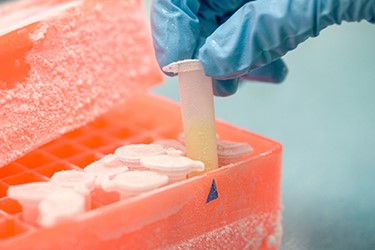
In clinical trials, the quality and integrity of the drug products and the biological samples are crucial for ensuring the validity and reliability of the results. However, maintaining the optimal storage conditions for these products can be challenging, especially when they must be transported or handled across different locations and environments.
Temperature excursions, which are deviations from the specified temperature range for a product or sample, can compromise the product's quality, safety, and efficacy and may have serious consequences for the trial outcomes, regulatory compliance, and patient safety. Therefore, clinical trial professionals must effectively prevent and manage temperature excursions, especially for temperature-sensitive products such as vaccines, biologics, and cell and gene therapies.
This article will provide an overview of temperature excursions, why avoiding them is essential, and how they can be prevented and managed in clinical trials. It will also offer some practical tips and tricks for cold chain management, which ensures that the product is kept within the required temperature range throughout the supply chain. By following the best practices and the guidance in this article, clinical trial professionals can reduce the risk and the impact of temperature excursions and ensure the quality and integrity of the product.
What Are Temperature Excursions, And Why Are They Important?
Temperature excursions are defined as any deviation from the specified temperature range for a product during transport, storage, or handling. The manufacturer or the sponsor usually determines the specified temperature range based on the stability data and the regulatory requirements for the product or sample. For example, some products may need to be stored at 2 degrees to 8 degrees C (refrigerated), while others may need to be stored at minus 20 degrees C or below (frozen).
Temperature excursions can occur due to various factors, such as weather delays, customs clearance, equipment failure, human error, or inadequate packaging or monitoring. Temperature excursions can affect the quality, safety, and efficacy of the product and may cause the following problems:
- Loss of potency or activity of the product may reduce its effectiveness or accuracy.
- Alteration of the physical or chemical properties of the product may affect its appearance, solubility, viscosity, or pH.
- Formation of aggregates, precipitates, or crystals in the product may compromise its stability or sterility.
- Generation of toxic or immunogenic substances in the product may pose a risk to the patient.
- Non-compliance with the regulatory standards or the trial protocols may result in audit findings, quality issues, or legal actions.
- Waste of resources, time, and money, as the product may need to be replaced, retested, or discarded.
Therefore, preventing and managing temperature excursions in clinical trials is essential, as they can have serious implications for trial outcomes, regulatory compliance, and patient safety.
How Do We Prevent Temperature Excursions?
The best way to prevent temperature excursions is to plan ahead and follow the best practices for cold chain management. Cold chain management ensures that the product is kept within the required temperature range throughout the supply chain, from the manufacturer or the sponsor to the site. Cold chain management involves selecting and validating the packaging and shipping materials, monitoring and tracking the temperature history, labeling and documenting the shipment, training and communicating with the staff, and coordinating and collaborating among the partners. Some of the tips and tricks to prevent temperature excursions are:
- Select the product's appropriate packaging and shipping materials based on the required temperature range, transit time, and destination. For example, you may use insulated containers, gel packs, dry ice, or liquid nitrogen to maintain the desired temperature during transport. You may also use passive or active packaging systems, depending on the level of control and automation you need. Passive packaging systems rely on preconditioned materials to maintain the temperature, while active packaging systems use electrical or mechanical devices to regulate the temperature. You should validate the performance and the suitability of the packaging and shipping materials before using them and follow the manufacturer's or the sponsor's instructions for their preparation and use.
- Use validated temperature monitors or indicators to track the temperature history of the shipment and alert the recipient of any potential excursions. Temperature monitors are devices that record or display the shipment temperature during transport, storage, or handling. They can be either electronic or chemical, and they can provide either continuous or single-point measurements. You should choose the type and the number of temperature monitors or indicators based on the product characteristics, the shipment size and duration, and the regulatory requirements. You should also validate the accuracy and reliability of the temperature monitors before using them and follow the manufacturer's or the sponsor's instructions for their placement and activation.
- Label the shipment clearly and accurately with the product name, storage conditions, and contact information. The label should indicate the product's name and description, the required temperature range for its storage, and the contact details of the sender and recipient. The label should also include any special instructions or warnings for the transport, storage, or handling of the product, such as "Do not freeze", "Keep upright", or "Protect from light". The label should be visible and legible and should be attached securely to the outer surface of the shipment. You should also include a copy of the label inside the shipment in case the outer label is damaged or lost.
- Train the staff involved in transporting, storing, and handling the product on the proper procedures and protocols. The staff should be familiar with the product characteristics, the packaging and shipping materials, the temperature monitors, the labeling and documentation, and the contingency plans for preventing and managing temperature excursions. The staff should also be aware of the potential risks and consequences of temperature excursions, as well as the importance of following the best practices and guidance for cold chain management. You should provide regular and updated training to the staff and evaluate their knowledge and performance periodically.
- Communicate and coordinate with the shipping partners, sites, and sponsors to ensure timely and secure delivery and receipt of the product. You should establish and maintain clear and effective communication and coordination with the shipping partners, such as the courier companies, the airlines, or the customs agents, to ensure that they understand and comply with the requirements and expectations for the transport, storage, and handling of the product. You should also inform and confirm with the sites, such as the clinics, the hospitals, or the laboratories, about the arrival and acceptance of the shipment and verify that they have the appropriate facilities and equipment to store and handle the product or sample. You should also report and update the sponsors, such as the manufacturers, the investigators, or the regulators, about the product's status and condition and notify them of any issues or incidents that may affect the quality and integrity of the product or sample.
How Do You Manage Temperature Excursions?
Despite the best efforts, temperature excursions may occur due to unforeseen circumstances, such as weather delays, customs clearance, equipment failure, or human error. In such cases, it is important to follow the steps below to manage the temperature excursions.
Report the excursion
Report the temperature excursion to the relevant stakeholders, most importantly the Analytical Development and Quality Control (ADQC) staff, as soon as possible and document the event's details, such as the date, time, duration, location, and temperature range. You should inform the sender, the recipient, and the sponsor of the temperature excursion as soon as you detect it and provide them with the relevant information and data from the temperature monitors. It would be best if you also documented any major temperature excursions in a written report, which should include the following information:
- the product or sample name, description, and batch or lot number,
- the shipment details, such as the origin, the destination, the transit time, and the carrier.
- the temperature excursion details, such as the date, time, duration, location, and temperature range,
- the temperature monitor or indicator details, such as the type, the number, the placement, and the readings,
- the actions taken to address the temperature excursion, such as the quarantine, the assessment, the CAPA, or the disposal, and
- the impact and the outcome of the temperature excursion, such as the product or sample status, the quality and safety issues, or the regulatory implications.
Quarantine the affected product until the ADQC department has performed the impact assessment and if needed, the corrective and preventive actions (CAPA) are completed. You should isolate the affected product from the rest of the shipment and store it in a separate and secure area within the required temperature range. You should also label the affected product as "Quarantined" or "Under Investigation" and restrict its access and use until the impact assessment. You should not release, distribute, or administer the affected product until you receive confirmation and approval from the sponsor or the manufacturer.
Read the instructions
Depending on the product that has experienced the temperature excursion, consult the product label, the package insert, the stability data, or the manufacturer or sponsor for guidance on the acceptability of the product after the temperature excursion. It would be best if you referred to the product label, the package insert, the stability data, or the manufacturer or sponsor for the information and the criteria on the acceptable temperature range, the maximum allowable excursion time, and the potential impact of the temperature excursion on the product quality, safety, and efficacy.
You should also follow the instructions and recommendations from the manufacturer or sponsor on handling and using the affected product after the temperature excursion. It would be best if you did not make any assumptions or decisions about the acceptability of the product without consulting the manufacturer or sponsor, as they are the ultimate authority and are responsible for the product’s quality and integrity.
Develop and execute a CAPA plan
Implement the CAPA plan to address the root cause of the temperature excursion, if needed, and prevent its recurrence. You should investigate and identify the root cause of the temperature excursion and analyze the contributing factors and the corrective actions that were taken. You should also develop and execute a CAPA plan, which should include the following elements:
- the objectives and scope of the CAPA plan, as well as the roles and responsibilities of the staff involved,
- the corrective actions to resolve the immediate problem and restore the regular operation,
- the preventive actions to eliminate or reduce the risk of the problem from happening again,
- the verification and validation of the effectiveness and the suitability of the corrective and preventive actions,
- the monitoring and evaluation of the performance and the outcome of the CAPA plan, and
- the documentation and communication of the CAPA plan and its results.
What To Do If The Product Is Unusable
If the product is deemed unusable or unsafe, you should discard the affected product safely and appropriately, following the local regulations and the sponsor's instructions.
You should also document and record the disposal of the product and provide the reason for and evidence of disposal. You should not use, distribute, or administer the product if deemed unusable or unsafe, as it may pose a risk to the trial outcomes, regulatory compliance, and patient safety.
About The Author:
Ana-Zeralda Canals Hamann is an associate director of clinical trial supplies at Debiopharm. She has more than a decade in sponsor-side pharmaceutical clinical operations, CMC, supply chain management, regulatory, IP, project management, and preclinical services. She earned her M.Sc. in clinical research administration and a Ph.D. in molecular medicine from the University of Oxford.