A Quality-Led Approach To Drug Production Facility Design
By Kate Coleman, VP regulatory affairs, quality and compliance, Arriello
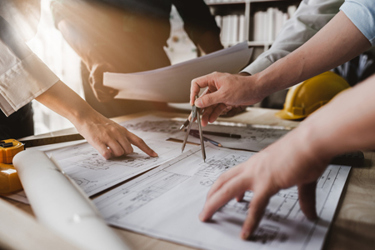
As drug development becomes more complex, and as regulations continue to evolve to maximize product quality and patient safety throughout production, meticulous manufacturing facility design is becoming ever more critical. Certainly, it is far better to design quality into the fabric of a building and its operational flow than to discover oversights and omissions when it is too late. There are a number of important considerations that can be missed if designs and their approval are left chiefly to architects and engineers, without the quality perspective as an integral contribution to discussions.
New biopharma production facilities are being established all the time. These could be greenfield sites resulting from new investment or a desire to boost supply resilience with a local production capability. They could be an extension of laboratory and warehousing operations or involve the repurposing and retrofitting of an existing brownfield site.
Looking Ahead: Designing For Future Site Use
Whatever the starting point, and whether the immediate use is for biologics including advanced therapy medicinal products (ATMPs) such as cell and gene therapies, active pharmaceutical ingredients (APIs), or finished drugs in oral solid dose form, it is worth considering how manufacturing facilities might be used over the longer term as initial designs are drawn up and agreed to.
Establishing compliant cleanroom facilities is of paramount importance to ensure that they are fit for purpose and support contamination control and segregation requirements. That’s in addition to product-specific requirements, such as containment to protect personnel and the external environment.
Selecting appropriate materials (e.g., for walls, windows, flooring) and considering their performance over the longer term are prudent and will save costs further down the line. Using the right materials supports qualification of the facility, particularly where disinfection is required and the materials may need to withstand regular application of potentially corrosive chemicals.
Futureproofing facilities may seem difficult when the future is unknown, but designing new facilities today that have the capability to change over time can make a significant difference to a company’s ability to be agile and to respond quickly to the ever-changing regulatory environment. Useful strategies to consider include designing ahead for higher cleanroom classification, for increased capacity, or in anticipation of how current/fallow production space might eventually be used.
Adopting A Preemptive Quality Risk Management Mindset
Although there is a balance to be struck, there is a good economic case for factoring in all possibilities from the start, especially given the ever-evolving regulatory landscape. In Europe, good manufacturing practice (GMP) is moving toward more proactive and “built-in” quality provision, so management becomes more preemptive, strategic, and inherent rather than a series of retrospective analyses and course corrections. Recent updates to GMP Annex 1, for instance, revolve around an infrastructural approach to quality risk management (QRM), via a detailed and extensive contamination control strategy (CCS). The U.S. has equivalent guidance, confirming that this is the way global regulation is leaning now.
Starting with a clean sheet with new or retrofitted premises gives manufacturers an opportunity to design quality into everything they do, from the building and its equipment to the way it fosters efficient, quality-compliant processes.
Common Oversights To Avoid
To underline the importance of a quality-led facility design, it’s useful to consider elements that are all too commonly overlooked when this perspective is excluded until a later point. Below are just a few examples:
- The heating, ventilation, and air conditioning (HVAC) design provides inadequate segregation and isolation of different manufacturing areas.
- Inadequate consideration of equipment movement into and out of the facility.
- Poor planning for pressure flows/relative room classifications; excessive wall erection/airlocks that are too small or poorly classified.
- The layout inhibits contamination control by encouraging poor flow/step retracing between clean and non-clean areas, making poor provision for the gowning process (e.g., sink positioning) or allowing insufficient space for “de-trashing” (removal of outer packaging).
- Airlocks/passthroughs are a common source of issues, often triggering redesign of facility elements when qualification exposes problems.
Forewarned Is Forearmed
Although production facility architects and engineers may display initial resistance to the involvement of quality professionals as part of the initial iterative design process, bringing in this vital perspective from day one mitigates the risk, delay, and additional cost of having to put things right once designs have been locked down and issued for construction.
While a specialist design/construction crew may claim to be experts in building facilities, particularly those for sterile or low bioburden products, allowing quality professionals to be a part of the process and to ask the right questions, in collaboration with architects/designers and engineers, will pay dividends. Those questions could be about the choices of materials, whether the proposed number of room partitions are really needed, whether the flow through the gowning area is going to be optimal from both a quality and a practical perspective, or what future use cases for the facility might be and therefore what additional considerations would be useful to plan in now. Challenging initial choices will help ensure that designs are right the first time, avoiding expensive retrofitting later.
Inviting someone with extensive shop-floor experience to walk through the building design using building information modelling (BIM) or a virtual reality (VR) representation of the envisaged facility, with a quality hat on, will help to catch any process dead ends or other points of risk before materials have been ordered. It could even save money if a provision for excessive partitions is foreseen (potentially compromising airlocks) or a specification for full glass walls (no good for photosensitive products) is designed out.
Conscious Risk Control
Enforcing focus on the “why?” of facility design fulfills a strong secondary purpose, too. Asking, challenging, and cementing decisions from the outset can serve as a powerful control in risk assessment, in that it will give rise to documented proof that quality risk mitigation has been designed in from the start – the right air changes, HVAC provision, etc. This demonstrates vigilance from day one, while negating the addition of new controls after the event.
Encouraging the early inclusion of quality-focused facilities design experts needn’t extend the planning timescales by very much at all, and it could save considerable delay and additional cost down the line.
About The Author:
Kate Coleman is VP of quality at Arriello. She has more than 20 years of experience in quality assurance, sterility assurance, and microbiology quality control and has worked across ATMPs, biologics, sterile fill/finish, vaccines, APIs, and oral dose platforms. Over her career to date, Coleman has served as a practicing Qualified Person (QP), principal consultant, and qualified lead auditor. She is also a subject matter expert in risk management, new facility design/start-up, and quality control. In her previous role before joining Arriello, she was senior director for quality management and compliance and head of QMC. Coleman can be reached by email at Kate.coleman@arriello.com.